This is my build thread from clio sport
Hey,
I'm Jack from MWMSport. This is my Ph1 172 that I bought shortly after Mike bought his.
I brought it for £600 off eBay with a snapped cambelt.
We started to rebuild the old engine but the cambelt snap had caused more damaged than we first thought.
We travelled from Staines too Carlisle on Christmas eve to collect the new engine and a set of Team Dynamics Pro Race 1.2's
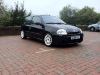
I fitted an exhaust, de-cat, Ktec engine mounts and some apex lowering springs just to get the ball rolling. I'm really impressed with the car and started using it for trackdays.
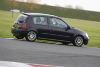
After sitting down the pub one night, having a bit of technical banter, we decided, pretty much just for the crack of it, to see what the engine would run like with a 197 inlet fitted as some people had said it wouldn't fit.
The results are, It does fit, it does improve power, but is probably not worth fitting as a sole modification.
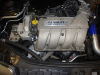
Now I have decided to see just how far you can push a standard engine with a turbo conversion. We believe we have found a way to safely and reliably lower the C/R of a standard engine to allow running bigger boost with a turbo.
We have 99% of the parts and are going to be starting the turbo build later on this week.
Well, Tuesday was the day the car came off the road for the turbo conversion. I didn't have to take the engine out to do this but i wanted to do the clutch, Paint the block and clean the engine bay so it just made life so much easier.
We pulled it in the workshop and took the engine out and the work begun.
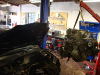
Next I put the engine on the engine stand, stripped it down and gave it a paint.
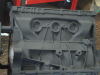
Then we steam cleaned out the engine bay
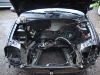
This is where the clever bit comes in!
We needed to find a way to cheaply lower the compression ratio that wouldn't compromise the reliability or strength of the engine.
After doing some work on a Clio 197 we noticed they use domed pistons but ran a similar compression ratio to the 182. After CCing the head the 197 head has a much bigger combustion chamber. Therefore bolting a 197 head on a 1*2 lowers the compression ratio!
In this picture you can see the difference in the 2 heads and where Renault Sport have removed the metal.
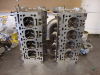
1*2
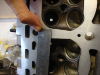
197
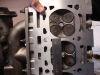
We have taken a scrap 1*2 head to the machine shop recently and it is possible to machine the combustion chamber to the same as a 197, so you do not have the cost of a 197 head and inlet manifold. That's just what we are using here as we were not sure the machining was possible at the time.
To run the 197 head we had to drill out and tap a bolt hole for the cambelt idler. this requires some proper measuring as it must be in the correct place.
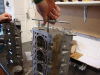
The next thing to do was to find and fit a supply pipe for the oil to the turbo. We have tee'd into the oil pressure swtich and got some custom line and fixings from think automotive.
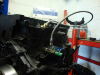
By the end of today we hope to have the head on and torque'd up, the turbo on the exhaust manifold and the oil return sorted.
UPDATE
The engine is almost ready to go back in!
We got everything back from the powder coaters for this car and the "soon to be supercharged" Car
I must say, I'm very very happy with the finish.
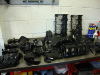
As the rocker cover was back we torque the head down and installed the cams.
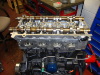
Next was the lower inlet, Megane 225 blue flag Injectors and the timing belt
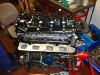
Now the upper inlet and a couple of brackets

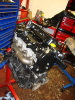
The modified sump will be ready at 2pm. That needs fitting then the engines going back in. We are trying to have it running well enough to come to the dyno day this Saturday!!!
Update From Todays Work
Today's work was a bit quite witch gave us some time to work on the Clio. Im happy to say we got a massive chunk out the way.
Firstly getting down to the business end of things was to fit the turbo!
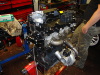
Once we had fitted the turbo we were quite worried of the engine was going to fit back in the bay as this turbos a bit of a big boy! Next we took the engine off the stand and fitted the flywheel, helix 4 padle clutch and the gearbox.
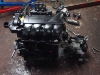
Next was to see if it would fit!
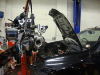
Shes in! With a fag papers width to spare!
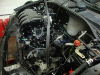
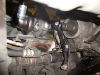
Were going to need to do some serious heat proofing around the bulkhead and possibly move the brake lines but apart from that shes there! We are getting a custom downpipe made Friday, then it will be live map the standalone ECU over night and make it to the dyno day saturday!
UPDATE!!!!!!!!
Before we did anything last night after finishing the paying jobs of the day, it was time for another BBQ! Weather was nice so why not?
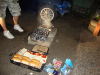
We mocked up the intercooler we are going to be using for now which is a standard Focus ST intercooler and worked out all the pipe work to get it to the turbo and inlet. One of my good mates is currently on a 250mile round trip to pick up the silicon hose’s to get the ready for mapping later.
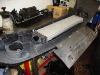
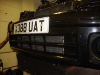
Standalone management was the next thing to go in. We have wired it in to trick the standard ecu into thinking it’s still running the engine. That way there shouldn't be any engine lights or the standard ECU interfering where it’s not wanted.
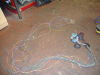
First things first was to pin out all the pins we needed from the standard ecu and let the chopping soldering and heat wrapping begin.
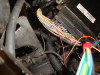
All completed and taped up. The loom running out the other side of the loom plug is the standalone loom.
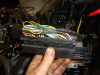
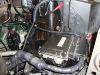
After a slight wiring mishap on the crankshaft sensor, (I'm letting us off that one as it was 2am and easily spotted at 8am after some sleep.) She runs on the standalone!!
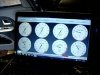
UPDATE-
Sorry for the slow update, those of you at the rolling road day will of seen that the made it there. It took an all nighter from Friday to Saturday. We were up for 36hours in total so please forgive us if you stank like a mouldy pond at the day! We dicided agastist putting it on the dyno just yet as we didn't have the boost sensitive FPR and were only running 6psi.
As we were rushing like mad I didn’t take many pictures as the build was drawing to an end.
This is a picture of the custom downpipe we had made. The space behind the engine is so tight, especially with the size turbo we are using so all the power steering pipe had to be moved as the brake lines.
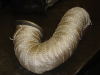
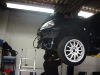
After working out the intercooler pipework the car flew back together. We started working on it at about 8pm after some food and it was all back together at 3.30-4am.
This is a video of it running up for the first time with +ve boost.
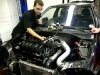
Hey,
I'm Jack from MWMSport. This is my Ph1 172 that I bought shortly after Mike bought his.
I brought it for £600 off eBay with a snapped cambelt.
We started to rebuild the old engine but the cambelt snap had caused more damaged than we first thought.
We travelled from Staines too Carlisle on Christmas eve to collect the new engine and a set of Team Dynamics Pro Race 1.2's
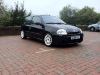
I fitted an exhaust, de-cat, Ktec engine mounts and some apex lowering springs just to get the ball rolling. I'm really impressed with the car and started using it for trackdays.
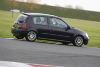
After sitting down the pub one night, having a bit of technical banter, we decided, pretty much just for the crack of it, to see what the engine would run like with a 197 inlet fitted as some people had said it wouldn't fit.
The results are, It does fit, it does improve power, but is probably not worth fitting as a sole modification.
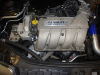
Now I have decided to see just how far you can push a standard engine with a turbo conversion. We believe we have found a way to safely and reliably lower the C/R of a standard engine to allow running bigger boost with a turbo.
We have 99% of the parts and are going to be starting the turbo build later on this week.
Well, Tuesday was the day the car came off the road for the turbo conversion. I didn't have to take the engine out to do this but i wanted to do the clutch, Paint the block and clean the engine bay so it just made life so much easier.
We pulled it in the workshop and took the engine out and the work begun.
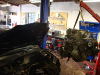
Next I put the engine on the engine stand, stripped it down and gave it a paint.
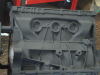
Then we steam cleaned out the engine bay
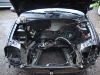
This is where the clever bit comes in!
We needed to find a way to cheaply lower the compression ratio that wouldn't compromise the reliability or strength of the engine.
After doing some work on a Clio 197 we noticed they use domed pistons but ran a similar compression ratio to the 182. After CCing the head the 197 head has a much bigger combustion chamber. Therefore bolting a 197 head on a 1*2 lowers the compression ratio!
In this picture you can see the difference in the 2 heads and where Renault Sport have removed the metal.
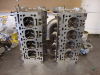
1*2
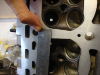
197
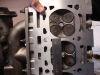
We have taken a scrap 1*2 head to the machine shop recently and it is possible to machine the combustion chamber to the same as a 197, so you do not have the cost of a 197 head and inlet manifold. That's just what we are using here as we were not sure the machining was possible at the time.
To run the 197 head we had to drill out and tap a bolt hole for the cambelt idler. this requires some proper measuring as it must be in the correct place.
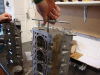
The next thing to do was to find and fit a supply pipe for the oil to the turbo. We have tee'd into the oil pressure swtich and got some custom line and fixings from think automotive.
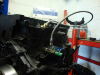
By the end of today we hope to have the head on and torque'd up, the turbo on the exhaust manifold and the oil return sorted.
UPDATE
The engine is almost ready to go back in!
We got everything back from the powder coaters for this car and the "soon to be supercharged" Car
I must say, I'm very very happy with the finish.
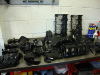
As the rocker cover was back we torque the head down and installed the cams.
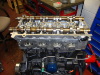
Next was the lower inlet, Megane 225 blue flag Injectors and the timing belt
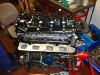
Now the upper inlet and a couple of brackets

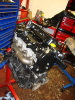
The modified sump will be ready at 2pm. That needs fitting then the engines going back in. We are trying to have it running well enough to come to the dyno day this Saturday!!!
Update From Todays Work
Today's work was a bit quite witch gave us some time to work on the Clio. Im happy to say we got a massive chunk out the way.
Firstly getting down to the business end of things was to fit the turbo!
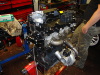
Once we had fitted the turbo we were quite worried of the engine was going to fit back in the bay as this turbos a bit of a big boy! Next we took the engine off the stand and fitted the flywheel, helix 4 padle clutch and the gearbox.
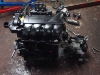
Next was to see if it would fit!
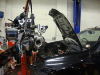
Shes in! With a fag papers width to spare!
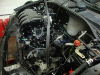
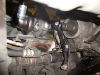
Were going to need to do some serious heat proofing around the bulkhead and possibly move the brake lines but apart from that shes there! We are getting a custom downpipe made Friday, then it will be live map the standalone ECU over night and make it to the dyno day saturday!
UPDATE!!!!!!!!
Before we did anything last night after finishing the paying jobs of the day, it was time for another BBQ! Weather was nice so why not?
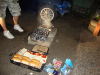
We mocked up the intercooler we are going to be using for now which is a standard Focus ST intercooler and worked out all the pipe work to get it to the turbo and inlet. One of my good mates is currently on a 250mile round trip to pick up the silicon hose’s to get the ready for mapping later.
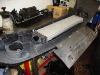
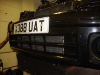
Standalone management was the next thing to go in. We have wired it in to trick the standard ecu into thinking it’s still running the engine. That way there shouldn't be any engine lights or the standard ECU interfering where it’s not wanted.
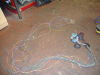
First things first was to pin out all the pins we needed from the standard ecu and let the chopping soldering and heat wrapping begin.
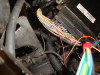
All completed and taped up. The loom running out the other side of the loom plug is the standalone loom.
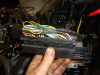
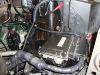
After a slight wiring mishap on the crankshaft sensor, (I'm letting us off that one as it was 2am and easily spotted at 8am after some sleep.) She runs on the standalone!!
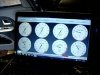
UPDATE-
Sorry for the slow update, those of you at the rolling road day will of seen that the made it there. It took an all nighter from Friday to Saturday. We were up for 36hours in total so please forgive us if you stank like a mouldy pond at the day! We dicided agastist putting it on the dyno just yet as we didn't have the boost sensitive FPR and were only running 6psi.
As we were rushing like mad I didn’t take many pictures as the build was drawing to an end.
This is a picture of the custom downpipe we had made. The space behind the engine is so tight, especially with the size turbo we are using so all the power steering pipe had to be moved as the brake lines.
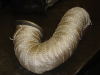
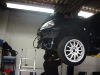
After working out the intercooler pipework the car flew back together. We started working on it at about 8pm after some food and it was all back together at 3.30-4am.
This is a video of it running up for the first time with +ve boost.
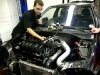