tombate911
Paid Member
Small update from this week and weekend.
Got the block dropped off at a new machine shop for them to rehone and have a look at the condition of the bores. The outcome of this was that the current piston to wall clearance is on average 0.06-0.07 but the bores are slightly tapered, not well honed and the machine shop are off the opinion that another 0.1 will be required to get the bores round and cylindrical. Taking the cylinder to wall clearance higher than the 0.15mm max spec from BMW. This would possibly lead to further issues in the future.
Off the back of this I spent the end of the week looking for a replacement block, actually found it very hard to find a replacement, kicking myself that I sold my old engine on for a good price last year! I really wish I hadn't now!
Found myself an engine as finding a decent block with main caps and front timing cover was harder than I expected.
Picked up the engine in the back of van.
Dirty old mess of an engine, according to the seller it was a unopened engine 100k miles.
I know my way around these pretty well now so it was easy pickings to get it stripped down, I just wanted to get a look inside the engine to see what the bores looked like and if the engine was even useable.
Cams out of the way the last step was to pull the head off.
With the head off it was clear to see the inside of the engine was nice and clear with the piston walls looking perfect.
At this point I was feeling pretty positive about the outcome here, however this was to be short lived.
Upon measuring the engine with a bore gauge it was clear that two of the cylinder was completely oval measuring less than 84mm front to back and over 84.2 across the exhaust to inlet side of the block.
We went back, checked the calibration of the equipment, measured the other bores again, still the same readings. Considering my old block had a max bore size of 84.02mm (0.07mm clearance)
Checked the main caps were torqued to spec, no difference to the readings.
We went down the route of exploring how much difference it makes having the head torqued down or using a torque place to simulate the pressure from the head being torqued. To do this with the crank removed I put the head back on with the old crushed head gaskets but dropped in my ARP headbolts with the longer thread engagement for the Aluminum M54 block and started to torque down the head studs so we could measure the bores from the underside with the crank removed.
Ping... Ping... Two of the studs never made it to 100nm as per ARP instructions and two of the threads pulled out of the block. The ARP's with the longer engagement are supposed to stop this, weirdly the two studs which did pull out were right next to the exhaust side of the most oval cylinder so I'm assuming that this engine has seen a lot of head at some point in it's life which has damaged the cylinders leading to them going oval as well as damaging the metal around the threads.
Did a quick measure of the bores from the underside and saw very little change in the bore dimensions, however it wasn't a perfect test due to two studs pulling the threads out of the block.
At the moment I now have reduced confidence in the torqueing down the head on the M54's even with the ARP's, however before that I don't even have a working block at the moment so I'm going to see what the machine shop recommend to stay within the BMW specs as well as keeping my eyes open for another block in the next few days but at the moment the E46 is retired for the remainder of the year until a reliable engine solution can be found and then I can build a new engine and go from there.
Got the block dropped off at a new machine shop for them to rehone and have a look at the condition of the bores. The outcome of this was that the current piston to wall clearance is on average 0.06-0.07 but the bores are slightly tapered, not well honed and the machine shop are off the opinion that another 0.1 will be required to get the bores round and cylindrical. Taking the cylinder to wall clearance higher than the 0.15mm max spec from BMW. This would possibly lead to further issues in the future.
Off the back of this I spent the end of the week looking for a replacement block, actually found it very hard to find a replacement, kicking myself that I sold my old engine on for a good price last year! I really wish I hadn't now!
Found myself an engine as finding a decent block with main caps and front timing cover was harder than I expected.
Picked up the engine in the back of van.
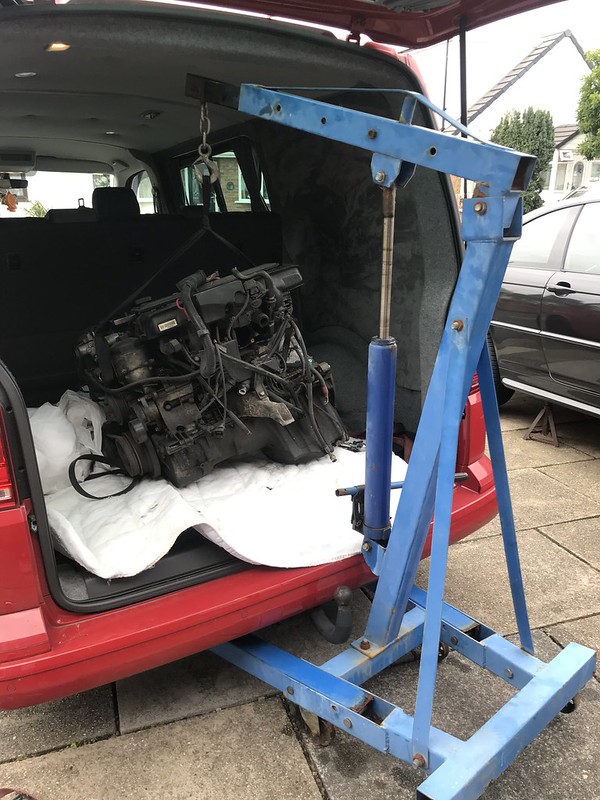
Dirty old mess of an engine, according to the seller it was a unopened engine 100k miles.
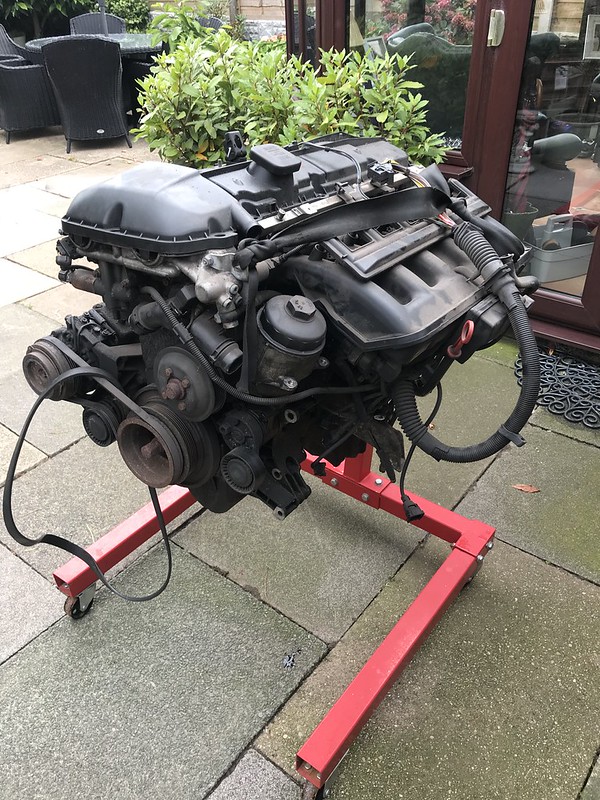
I know my way around these pretty well now so it was easy pickings to get it stripped down, I just wanted to get a look inside the engine to see what the bores looked like and if the engine was even useable.
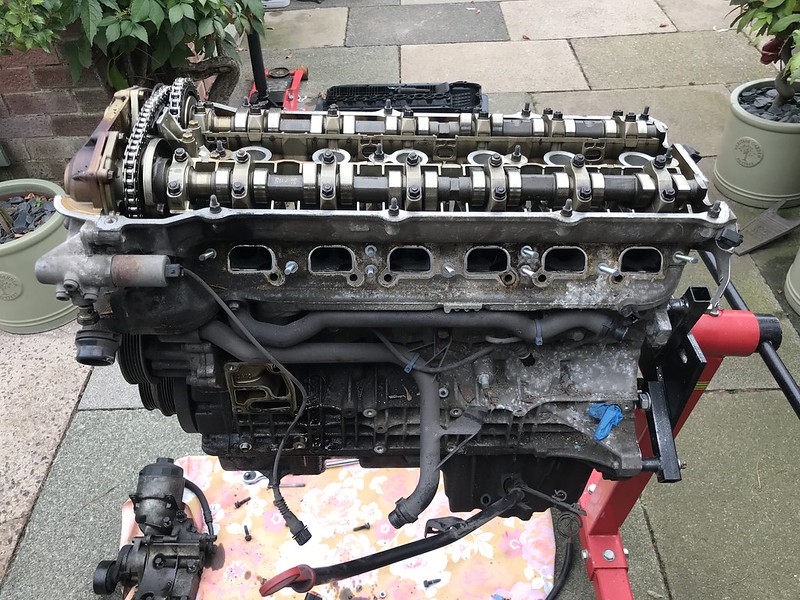
Cams out of the way the last step was to pull the head off.
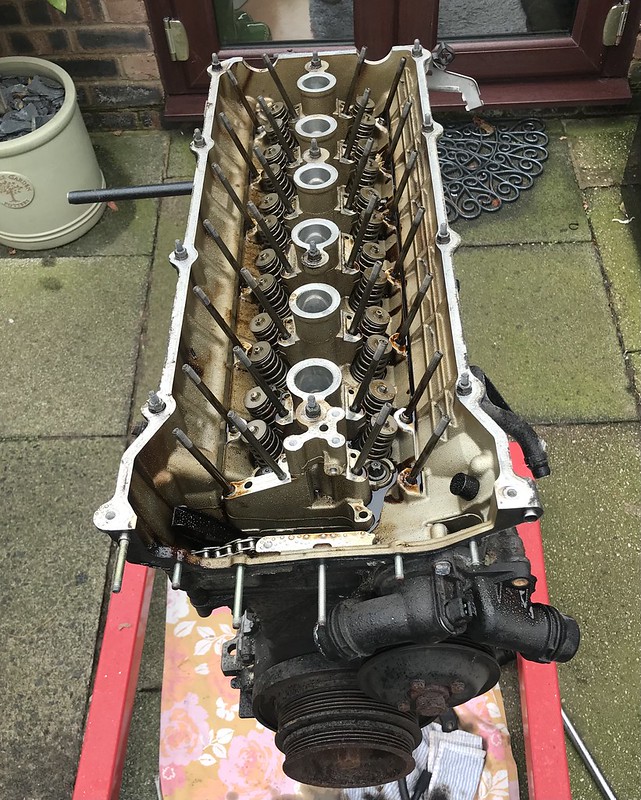
With the head off it was clear to see the inside of the engine was nice and clear with the piston walls looking perfect.
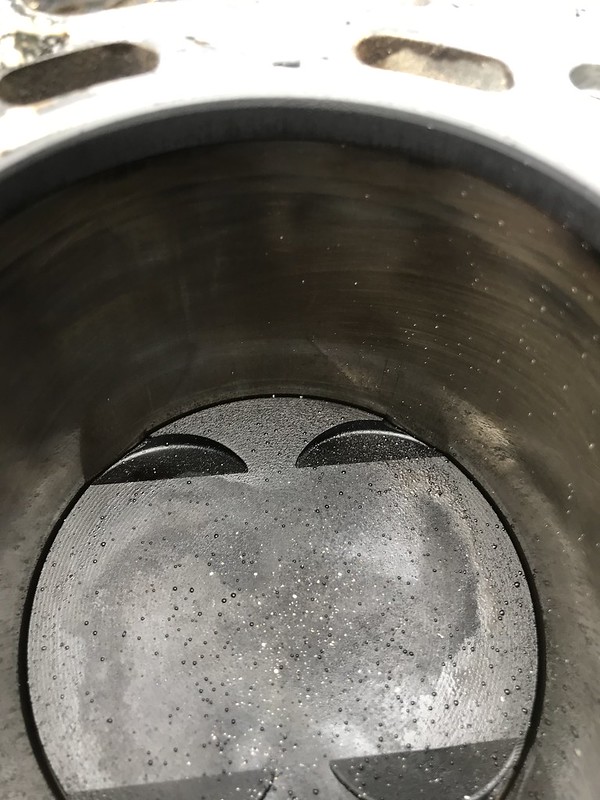
At this point I was feeling pretty positive about the outcome here, however this was to be short lived.
Upon measuring the engine with a bore gauge it was clear that two of the cylinder was completely oval measuring less than 84mm front to back and over 84.2 across the exhaust to inlet side of the block.
We went back, checked the calibration of the equipment, measured the other bores again, still the same readings. Considering my old block had a max bore size of 84.02mm (0.07mm clearance)
Checked the main caps were torqued to spec, no difference to the readings.
We went down the route of exploring how much difference it makes having the head torqued down or using a torque place to simulate the pressure from the head being torqued. To do this with the crank removed I put the head back on with the old crushed head gaskets but dropped in my ARP headbolts with the longer thread engagement for the Aluminum M54 block and started to torque down the head studs so we could measure the bores from the underside with the crank removed.
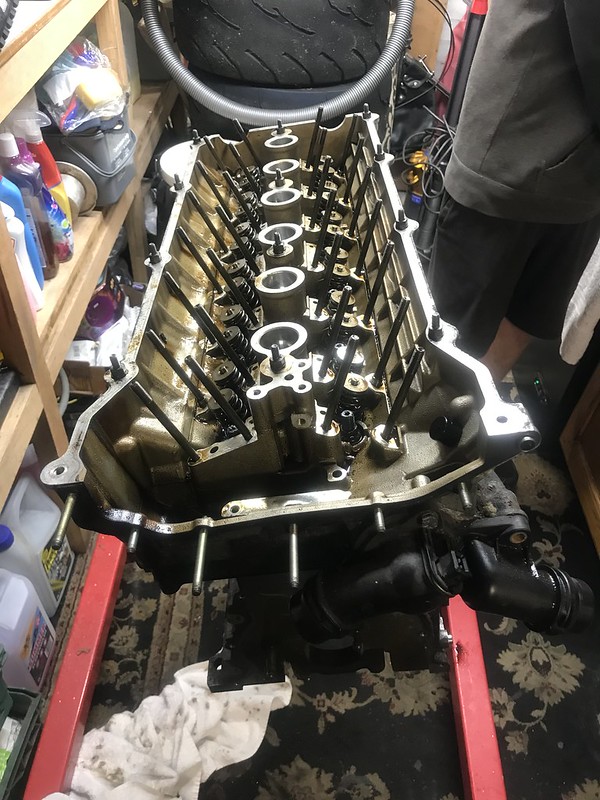
Ping... Ping... Two of the studs never made it to 100nm as per ARP instructions and two of the threads pulled out of the block. The ARP's with the longer engagement are supposed to stop this, weirdly the two studs which did pull out were right next to the exhaust side of the most oval cylinder so I'm assuming that this engine has seen a lot of head at some point in it's life which has damaged the cylinders leading to them going oval as well as damaging the metal around the threads.
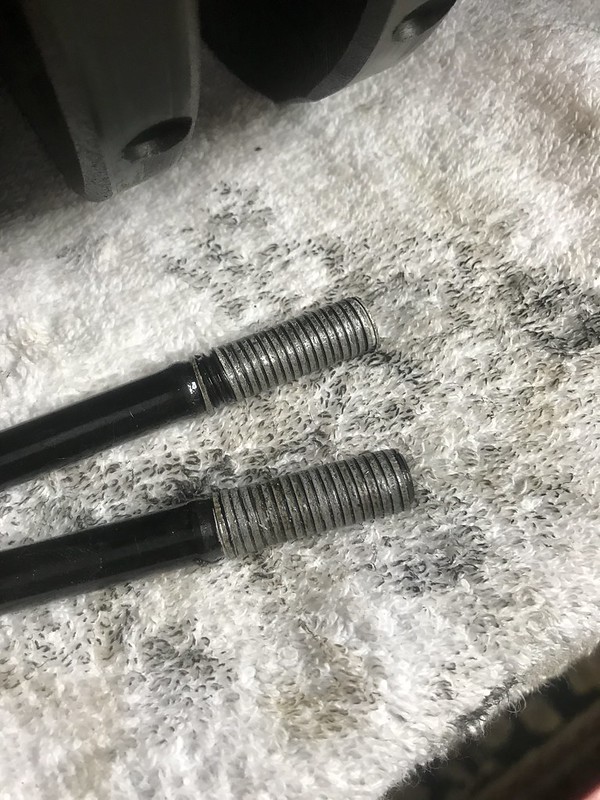
Did a quick measure of the bores from the underside and saw very little change in the bore dimensions, however it wasn't a perfect test due to two studs pulling the threads out of the block.
At the moment I now have reduced confidence in the torqueing down the head on the M54's even with the ARP's, however before that I don't even have a working block at the moment so I'm going to see what the machine shop recommend to stay within the BMW specs as well as keeping my eyes open for another block in the next few days but at the moment the E46 is retired for the remainder of the year until a reliable engine solution can be found and then I can build a new engine and go from there.