tomislavp4
Paid Member
Hi guys. I'm running some CFD simulations on a model of a 197 in my spare time and wanted to open a thread so I can share the results with you. The goal is to see what aftermarket parts work and how well they work. Later on I will test out some custom stuff (wings, splitters etc.) as well. Now keep in mind that I am not a professional aerodynamicist so take this with a grain of salt.
The simulations are done on a half-a-car model with sealed engine bay and partially modeled underbody. Models of this kind are usually used by carmakers early on in the concept design stage for comparing different shapes. As these simulations are highly simplified, they tend to underestimate the drag coefficient and overestimate the lift coefficient.
Beow are pictures of the "stock" and the "cup" model used in the simulations and the results.
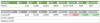
The stock model has a drag coefficient of 0,365 and a lift coefficient of -0,261 which gives a lift to drag ratio of -0,715. The drag figure is in the normal range for hatchbacks. The lift value however is very optimistic. It means that the downforce produced by the car at top speed is 130 kg which is highly unlikely. As mentioned before, the simulations overestimate the lift values.
The Cup spoiler and splitter increase the drag coefficient by 19 percent but they also increase the lift coefficient by 54,8 percent. The lift to drag ratio goes up 30,1 percent so the car is more efficient at producing downforce with the Cup bits but it will have a lower top speed.
To see what is happening with the flow, I've attached pictures of the pressure and velocity on the symmetry plane as well as pressure on the models themselves. We can clearly see how the spoiler creates a high pressure area in front of it and how it alters the shape of the wake.
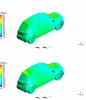
To better see the effects of the spoiler I have pictures of low pressure areas on the symmetry plane and the underbody of the models. The stock car has a region of lower pressure on the front of the underbody but the Cup car has greater area for the low pressure to act on. At the back of the car, it is clear that the low pressure zones are bigger on the Cup car so the aerodynamic balance should be shifted backwards.
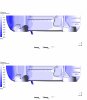
Now you can say that you can make these pictures in photoshop or paint even, and you'd be correct. There's no way to verify this stuff so that we can be sure it is in the ballpark of reality. One thing we can do is estimate the drag coefficient from available data and see how close the drag value from the simulation is to it. Assuming 15 percent drivetrain loss and 0,02 coefficient of rolling friction we can estimate the drag coefficient to 0,371. Close enough for me.
Will be posting more stuff as soon as I complete more simulations. Cheers!
The simulations are done on a half-a-car model with sealed engine bay and partially modeled underbody. Models of this kind are usually used by carmakers early on in the concept design stage for comparing different shapes. As these simulations are highly simplified, they tend to underestimate the drag coefficient and overestimate the lift coefficient.
Beow are pictures of the "stock" and the "cup" model used in the simulations and the results.
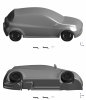
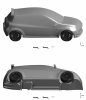
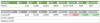
The stock model has a drag coefficient of 0,365 and a lift coefficient of -0,261 which gives a lift to drag ratio of -0,715. The drag figure is in the normal range for hatchbacks. The lift value however is very optimistic. It means that the downforce produced by the car at top speed is 130 kg which is highly unlikely. As mentioned before, the simulations overestimate the lift values.
The Cup spoiler and splitter increase the drag coefficient by 19 percent but they also increase the lift coefficient by 54,8 percent. The lift to drag ratio goes up 30,1 percent so the car is more efficient at producing downforce with the Cup bits but it will have a lower top speed.
To see what is happening with the flow, I've attached pictures of the pressure and velocity on the symmetry plane as well as pressure on the models themselves. We can clearly see how the spoiler creates a high pressure area in front of it and how it alters the shape of the wake.
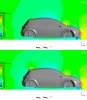
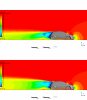
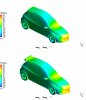
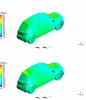
To better see the effects of the spoiler I have pictures of low pressure areas on the symmetry plane and the underbody of the models. The stock car has a region of lower pressure on the front of the underbody but the Cup car has greater area for the low pressure to act on. At the back of the car, it is clear that the low pressure zones are bigger on the Cup car so the aerodynamic balance should be shifted backwards.
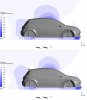
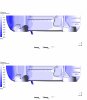
Now you can say that you can make these pictures in photoshop or paint even, and you'd be correct. There's no way to verify this stuff so that we can be sure it is in the ballpark of reality. One thing we can do is estimate the drag coefficient from available data and see how close the drag value from the simulation is to it. Assuming 15 percent drivetrain loss and 0,02 coefficient of rolling friction we can estimate the drag coefficient to 0,371. Close enough for me.
Will be posting more stuff as soon as I complete more simulations. Cheers!