TB Rich
Paid Member
Hi guys,
Anyone here work in a shop with CNC access? I am wondering how much the following mount would cost to make, ideally some form of alloy billet - it's about 4 inches long, 2 inches wide, 2 inches high. I would need 8.
I've just been messing around in FreeCAD for now, need to mock them in wood first to check dimensions but I have no idea how much this kinda thing would cost??
They are to go between the OMP subframe and Recaro seat sliders to fix the offset issue with the seats and therefore hopefully get my stupid ******* Recaro's finally installed!!
Cheers
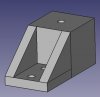
Anyone here work in a shop with CNC access? I am wondering how much the following mount would cost to make, ideally some form of alloy billet - it's about 4 inches long, 2 inches wide, 2 inches high. I would need 8.
I've just been messing around in FreeCAD for now, need to mock them in wood first to check dimensions but I have no idea how much this kinda thing would cost??
They are to go between the OMP subframe and Recaro seat sliders to fix the offset issue with the seats and therefore hopefully get my stupid ******* Recaro's finally installed!!
Cheers
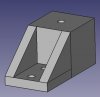